- CarbonStorage.io
- Posts
- DOE cancels 24 low carbon projects | Deep Dive
DOE cancels 24 low carbon projects | Deep Dive
Special edition to cover the cancellation of DOE funded projects

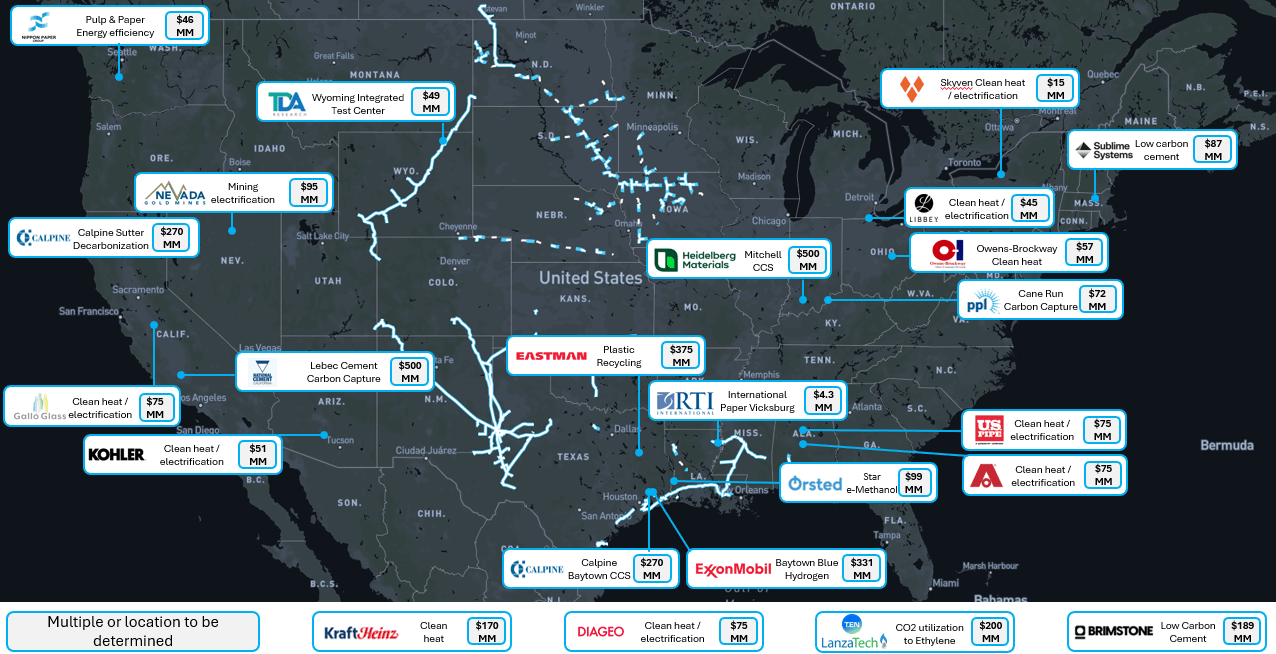
The Department of Energy has canceled 24 awards from the Office of Clean Energy Demonstrations, cutting over $3.7 billion in cost-shared funding.
Spanning sectors such as carbon capture, low-carbon cement, and industrial clean heat for pulp and paper, heavy manufacturing, and food and beverage, the affected projects represent major decarbonization efforts.
This decision creates uncertainty, as many initiatives had already secured commercial offtake agreements, industry partnerships, and substantial private investment.
A good example of this is Sublime Systems, a company that’s redesigning low carbon cement. Last month, they signed a binding agreement with Microsoft to sell 623,000 tons of green cement from their Holyoke facility.
ExxonMobil | Baytown Hydrogen | $331.9 million
ExxonMobil’s Baytown Olefins Plant Carbon Reduction Project aims to replace natural gas with up to 95% clean hydrogen in high-temperature ethylene production using new burner technologies. The project could cut 2.7 million metric tons of CO₂ and 200 tons of NOx emissions annually—over half the plant’s total emissions. As one of the largest U.S. ethylene facilities, this project would demonstrate the feasibility of clean hydrogen in heavy industry and support decarbonization across the chemical sector.
Last month, ExxonMobil announced an Ammonia offtake agreement with Marubeni to supply 250,000 tons to Japan
Last September, ADNOC acquired a 35% equity stake in the Baytown project
In January, ExxonMobil and Trammo signed an Heads of Agreement to supply 300,000 - 500,000 metric tons of ammonia per year
Project partners include Air Liquide to supply Air Separation Units, Technip Energies for FEED, and Topsoe for Autothermal reforming technology
Nippon Dynawave Packaging | $46.6 million
Nippon Dynawave Packaging and Via Separations are partnering to decarbonize a thermal process at NDP’s Longview, WA facility by implementing Via’s ARPA-E-supported membrane technology. The project aims to reduce CO₂ emissions by 70% per gallon of water removed during pulp production, significantly improving energy efficiency. It also serves as a demonstration of the technology's potential for broader adoption across the pulp and paper industry and other sectors like chemical manufacturing.
Eastman Chemical | Longview | $375 million
Eastman Chemical plans to build a pioneering molecular recycling facility in Longview, Texas to convert hard-to-recycle plastics into virgin-quality PET. The project will use on-site solar power and thermal energy storage to decarbonize high-temperature process heat, cutting the product’s carbon intensity by 70% compared to fossil-based PET.
The investment is expected to bring over 200 full-time, high-paying jobs to the Longview community in addition to approximately 1,000 temporary construction jobs during site development and building of the facility.
Orsted | Star e-Methanol | $99 million
Ørsted’s Star e-Methanol project will produce up to 300,000 metric tons of e-methanol annually using captured CO₂ and clean hydrogen, aiming to cut greenhouse gas emissions by over 80% compared to conventional methods. Targeting hard-to-electrify sectors like shipping, the project demonstrates the viability of clean hydrogen fuels. Ørsted will source hydrogen from the Gulf Coast Hydrogen Hub (HyVelocity), where it is also a participant.
Technip Energies & LanzaTech | CO2 utilization to Ethylene | $200 million
Technip Energies and LanzaTech plan to demonstrate a biotech-based process that converts captured CO₂ from ethylene production into sustainable ethanol and ethylene using low-carbon hydrogen. LanzaTech’s gas fermentation technology can be applied across industries to recycle carbon-rich waste streams, offering an alternative to emissions or carbon sequestration.
Power Generation
Calpine | Baytown |
Calpine's Baytown CCS Project will be the first full-scale carbon capture facility at a U.S. natural gas combined-cycle power plant. Using Shell’s CANSOLV technology, it aims to capture up to 2 million metric tons of CO₂ annually from the Baytown Energy Center and store it in Gulf Coast saline formations. The project also plans to reduce water use with greywater cooling and support industrial decarbonization through its offtake partner, Covestro, which will utilize low-carbon power and steam.
In April, ExxonMobil & Calpine signed a CO2 transportation and storage agreement for 2.0 million tons per year
In March 2023, Shell Catalysts & Technologies, together with Technip Energies and Zachry Group (Zachry), was awarded a front-end engineering and design (FEED) contract
Calpine | Sutter |
Calpine’s Sutter Decarbonization Project will develop a commercial-scale carbon capture and storage (CCS) facility, targeting up to 1.75 million metric tons of CO₂ captured annually.
ION Clean Energy was selected as the capture technology in December 2023
PPL | Cane Run | $72 million
The project aims to capture over 95% of CO₂ emissions from up to 20 megawatts of the plant’s 691 MW capacity, potentially reducing emissions by approximately 67,000 metric tons annually. Developed in collaboration with the University of Kentucky, the Electric Power Research Institute, and other partners, the initiative will utilize advanced heat-integrated CO₂ capture technology. The captured CO₂ is planned to be purified and entirely reused by a nearby industrial customer
Technology and EPC providers include Siemens Energy and Kiewit
Nevada Gold Mines | $95 million
Nevada Gold Mines (NGM), a joint venture between Barrick and Newmont, has secured up to $95 million in federal funding from the U.S. Department of Energy to develop solar and battery storage systems at its Turquoise Ridge and Cortez mining sites. The project will install a combined 100 MW of solar PV and 248 MWh of battery energy storage, aiming to cut approximately 2 million tons of CO₂ emissions over its lifetime.
Kraft Heinz | $170 million
Kraft Heinz plans to decarbonize process heat at up to 11 facilities through its "Delicious Decarbonization Through Integrated Technologies" project by using electric heaters, boilers, heat pumps, and renewable energy. If fully implemented, the project could cut over 100,000 metric tons of CO₂ annually. It aims to demonstrate how integrated technologies can lower emissions and energy costs across the U.S. food and beverage sector.
Diageo | $75 million
Diageo, in partnership with Rondo Energy and NREL, plans to decarbonize its beverage production facilities in Kentucky and Illinois by replacing natural gas heat with Rondo Heat Batteries, electric boilers, and renewable-powered thermal systems. The upgrades aim to cut emissions by nearly 14,000 metric tons annually and offer a replicable model for using thermal batteries with intermittent renewable energy in manufacturing.
Libbey Glass | $45 million
Libbey Glass plans to cut carbon emissions at its Toledo, OH facility by up to 50% by replacing four furnaces with two hybrid electric ones that use up to 80% electricity for melting. The project will also reduce air pollutants like NOx, SOx, and particulates, improving local air quality. As a producer of high-standard glass tableware, Libbey's project could demonstrate the broader potential of electrification and alternative fuels in the glass industry.
Owens-Brockway Glass Container | $56 million
O-I Glass plans to rebuild a furnace at its Zanesville, OH facility to cut carbon intensity by 20–40% using a combination of five advanced decarbonization technologies—such as heat recovery, fuel system upgrades, material pre-heating, and electric conversions. This will be the first time all five are deployed together, aiming to lower energy use and CO₂ emissions. The project could showcase a scalable, multi-technology model for decarbonizing glass production across various products.
Gallo Glass Company | $75 million
Gallo Glass plans to install a hybrid electric furnace to cut natural gas use by up to 70% and reduce carbon intensity by over 40% in its glass bottle production. The project will also boost recycled content and use low-carbon energy sources. Gallo aims to offer low-carbon bottles as a premium product, supporting decarbonization across California’s wine and spirits packaging industry.
Process Heat:
Skyven Technologies | $145 million
Skyven Technologies aims to decarbonize industrial steam production through its "heat-as-a-service" model, starting with Western New York Energy in Medina, NY. By replacing natural gas boilers with steam-generating heat pumps, the project will electrify process heat and demonstrate a scalable, cross-sector solution for reducing fossil fuel reliance in energy-intensive manufacturing.
Kohler | $51.2 million
Kohler plans to decarbonize its Vikrell fixture facility in Casa Grande, AZ by installing electric boilers and a microgrid with 21 MW of solar and 20.5 MW of battery storage. The project aims to cut process heat CO₂ emissions by 75–90%, or about 7,865 metric tons annually. It will showcase how renewables and microgrids can reduce industrial emissions while maintaining operational flexibility and economic efficiency.
National Cement Company of California | Lebac Net-Zero | $500 million
The Lebec Net Zero Project aims to produce carbon-neutral cement at NCC-CA’s Lebec, CA plant by combining three strategies: replacing fossil fuels with agricultural biomass, producing lower-carbon LC3 cement, and capturing and storing up to 950,000 metric tons of CO₂ annually. The project demonstrates how integrated decarbonization approaches can bring existing U.S. cement facilities to net-zero emissions.
In March, Carbon TerraVault (California Resources Corporation) announced an MOU with National Cement to transport and store 1 million tons per year
Heidelberg Materials | Mitchell Plant | $500 million
Heidelberg Materials plans to deploy carbon capture and storage at its Mitchell, IN cement plant to capture at least 95% of CO₂ emissions—up to 2 million tons annually. The captured CO₂ will be stored in geological formations beneath the site. As one of the first CCS projects for a U.S. cement plant, it aims to demonstrate a scalable decarbonization pathway for the industry.
Earlier this year, Heidelberg drilled and tested a CO2 injection well for CO2 storage
In addition to carbon capture funding, the project has also received CarbonSAFE funding for sequestration
Brimstone Commercial | $189 million
Brimstone plans to build a commercial-scale plant to produce 103,000 metric tons annually of decarbonized Portland cement, supplementary materials, and smelter-grade alumina. By using calcium silicate rocks and alternative methods, the project aims to cut over 77,000 metric tons of CO₂ emissions per year. It builds on ARPA-E-supported research and aims to prove the technical and commercial viability of low-carbon industrial manufacturing.
Sublime Systems | $87 million
Sublime Systems plans to build a low-carbon cement plant in Holyoke, MA using an electrochemical process that replaces limestone with calcium silicate feedstock, eliminating the need for high heat. The project aims to produce industry-standard cement with minimal emissions, strengthen U.S. low-carbon supply chains, and drive broader decarbonization across the cement industry.
Sublime has signed binding, long-term agreements with Microsoft to purchase up to 623,000 tons of green cement
United States Pipe and Foundry Company | $75 million
U.S. Pipe plans to replace a coke-fired furnace with electric induction furnaces at its Alabama facility, cutting gate-to-gate carbon intensity by over 70% and eliminating the use of natural gas and coal-based coke. The project will improve air quality by reducing particulate matter and other pollutants, lower operating costs, and boost manufacturing efficiency—demonstrating the potential to electrify core processes in iron and steel production.
AMERICAN Cast Iron Pipe Company | $75 million
AMERICAN Cast Iron Pipe Company plans to replace a coke-fired cupola furnace with four electric induction furnaces at its Birmingham, AL facility, cutting melt process CO₂ emissions by about 95%. The project aims to decarbonize ductile iron pipe production, reduce air pollutants, and provide lower-carbon piping for municipal water systems and new industrial developments like chip and battery plants.
